Tech and Trends
The Nearshoring Experiment: Resilient Supply Chains or a Work in Progress?
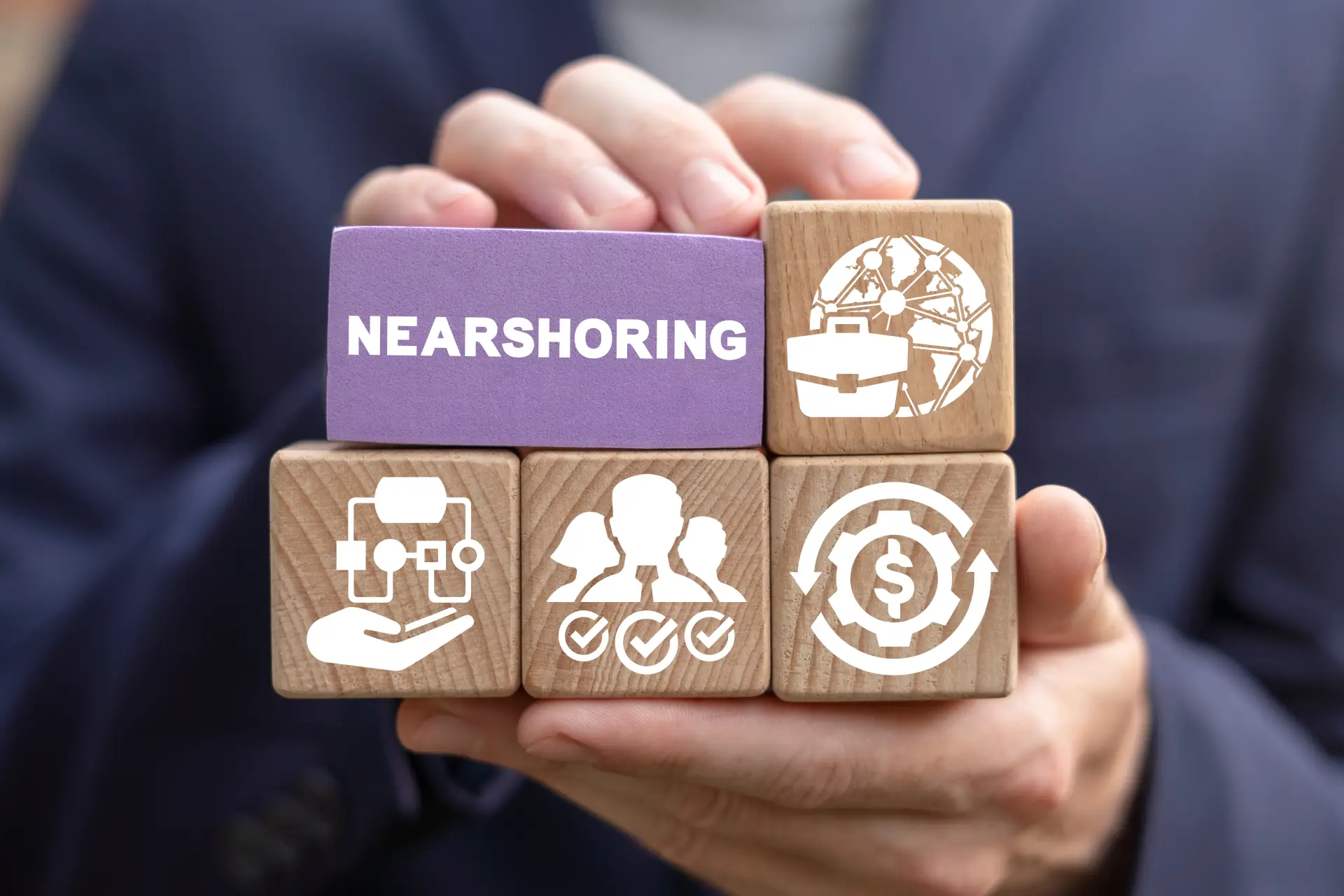
The end of 2024 bore an eerie resemblance to the conclusion of 2019, marked by unsettling headlines about the spread of the Human Metapneumovirus (HMPV). To compound the challenges, President Donald Trump’s announcement of tariffs on imports from Mexico, Canada, and other trade partners has set the stage for potential economic turbulence. These twin developments are testing the resilience of global supply chains once again.
How Much Has Changed Since 2019-20?
The COVID-19 pandemic was a watershed moment for global supply chains. Companies learned the hard way that efficiency-driven models dependent on distant, single-region sourcing were highly susceptible to disruption. Nearshoring and reshoring emerged as viable alternatives, promising reduced lead times, greater control, and enhanced resilience. But how much has actually changed since then?
Shifting Supply Chains: The Data Speaks
Initial nearshoring and reshoring efforts in the US and EU aimed to address vulnerabilities exposed by the pandemic. According to Fictiv’s 2024 State of Manufacturing survey, 54% of North American manufacturers adopted nearshoring strategies, while 66% increased onshoring efforts. The result: imports from China declined by 14% between 2019 and 2023, while Mexico’s manufacturing exports to the US surged by 20%, benefiting industries like automotive and consumer goods.
Europe mirrored these efforts, leveraging Central and Eastern Europe as well as Mediterranean nations such as Turkey and Morocco for nearshoring. Yet, progress has plateaued. By late 2024, the resurgence of trade with China signaled a shift back to reliance on Asia. QIMA data revealed a 21% year-over-year increase in inspections and audits in China by US and EU buyers during Q3 2024, driven by demand for electronics (+41%), homewares (+22%), and textiles (+23%).
This trend reflects not only economic pragmatism but also the ongoing challenges of fully transitioning to local supply chains. Gaps in infrastructure, talent shortages, and high costs in nearshoring destinations have slowed the momentum of reshoring efforts.
High-Impact Sectors: Automotive, Aerospace, and Electric Vehicles
The automotive industry exemplifies the tension between nearshoring aspirations and entrenched dependencies. While companies like Ford and General Motors expanded operations in Mexico, established Chinese supply chains—such as Volkswagen’s—remain deeply integrated. Supply chain disruptions persisted in 2024, with 90% of respondents in McKinsey’s Global Supply Chain Leader Survey reporting ongoing challenges.
Electric vehicles (EVs) highlight another critical hurdle. China’s dominance in rare earth materials and battery components complicates nearshoring in this sector. The US CHIPS and Science Act aimed to boost domestic semiconductor production, but progress has been slow. Meanwhile, Intel’s Ohio factories, announced in 2022, are years away from alleviating chip shortages.
The aerospace industry reflects similar complexities. Boeing’s reliance on global networks for specialized parts has resulted in months-long delays. Transitioning to nearshored suppliers involves significant time and certification processes, underscoring the global interdependence that still defines this sector.
The HMPV Disruption: Lessons (Un)Learned?
HMPV’s outbreak in late 2024 has reignited concerns about global supply chain preparedness. Images of overwhelmed hospitals and social media’s rapid dissemination of the crisis brought a sense of déjà vu. It quickly became evident that despite the lessons of COVID-19, many businesses remain vulnerable to unforeseen shocks. The resurgence of sourcing activity in China in 2023-24 further highlights the limited progress in diversifying supply chains.
Barriers to Nearshoring: Costs and Complexity
While nearshoring offers theoretical advantages, practical challenges remain significant. Bain & Company’s survey indicates that 70% of retailers plan to increase nearshoring, but high relocation costs and labor shortages in destinations like Mexico and Eastern Europe hinder progress. Additionally, labor costs in nearshoring regions, though lower than in the US, cannot compete with Asia’s ultra-low-cost economies. Infrastructure deficits and supplier development requirements compound these issues.
Reshoring to the US faces its own hurdles. Decades of offshoring have eroded domestic manufacturing expertise, creating a substantial skills gap. Advanced manufacturing now requires proficiency in robotics, automation, and AI, skills that remain scarce. High labor costs and an aging workforce further challenge reshoring’s feasibility without significant investments in workforce development.
China’s Pivotal Role: A Compelling Pragmatism
China’s role as a global sourcing partner remains critical, and recent developments underscore its enduring significance. QIMA data inspections and audits in China ordered by European businesses increased significantly: 27% year-over-year from Germany and 32% from the UK. US buyers, while more measured, still increased inspections in China by 13%. China’s robust infrastructure, skilled workforce, and cost efficiency ensure its continued appeal despite geopolitical tensions.
While direct imports into the US from China decreased, Chinese companies capitalized on the nearshoring trend in the US by increasing their exports to Mexico. Data shows an 18.9% increase in container trade between China and Mexico from January to September 2024, following a 34.8% growth in 2023 and 3.5% growth in 2022. This surge is partly driven by Chinese companies relocating production to Mexico to leverage the USMCA trade benefits. By manufacturing in Mexico using Chinese components, companies have been able to designate products as “Made in Mexico,” avoiding US tariffs while reducing costs. This strategy has reshaped supply chains, particularly in sectors like automobiles, electronics, and textiles.
Chinese firms are also taking advantage of Mexico’s extensive trade agreements, which span 50 countries, to access global markets more efficiently. This “China Plus One” strategy—combining operations in China with nearshoring in Mexico—provides resilience against geopolitical tensions and tariff uncertainties. As a result, Mexico’s exports to the US have seen consistent growth, supported by a record USD 36.1 billion in foreign direct investment in 2023 and continued momentum into 2024. The logistical efficiencies of shipping through Mexico’s ports and crossing into the US by rail or truck further enhanced this route’s attractiveness.
However, the recent announcement of potential new tariffs on Mexican imports adds an unpredictable element. These tariffs could undermine the economic advantages of nearshoring in Mexico and disrupt established supply chains. Companies relying on the Mexico-China-US trade route may face higher costs and delays, potentially prompting a re-evaluation of their strategies. While some firms might shift back to Asian sourcing, others could double down on regional diversification to mitigate risks. The outcome is likely to hinge on the severity and scope of the tariffs as well as companies’ ability to adapt to changing trade policies.
A Shift Toward Resilience and Sustainability
Despite these varied patterns, it is undeniable that nearshoring aligns with broader trends toward resilience and sustainability, offering companies a chance to rebuild supply chains with an eye on long-term environmental and social goals. Shorter supply chains reduce carbon footprints by minimizing transportation distances and associated emissions. By moving production closer to consumer markets, companies can better monitor compliance with ethical labor practices and environmental standards.
The push for sustainability extends beyond logistics. Smart factories and green technologies are becoming central to nearshoring initiatives. These facilities leverage renewable energy, automation, and IoT-enabled systems to optimize efficiency while adhering to stricter environmental guidelines. Companies like Tesla and BMW, which are expanding operations in Mexico, are incorporating these technologies into their new facilities, signaling a shift toward greener manufacturing.
However, sustainability efforts must be balanced against the economic realities of nearshoring. Higher production costs in nearshoring destinations compared to Asia remain a challenge, underscoring the need for innovations that reduce expenses without compromising environmental goals. In countries pursuing these polices, the government and the private sector must collaborate to develop incentives and invest in infrastructure that supports the viability of sustainable nearshoring.
Beyond Nearshoring: A Hybrid Approach
For many businesses, a hybrid model balancing nearshoring, offshoring, and onshoring offers the best path forward. By segmenting supply chains based on product needs, companies can achieve an equilibrium between cost, resilience, and sustainability. This strategy allows for adaptability in an unpredictable global landscape.
Transformation or A Temporary Trend?
The data highlights both the potential and the limitations of nearshoring and reshoring. While the initial surge reflected a desire for resilience, the re-emergence of trade with China and persistent barriers suggest that progress has been uneven. Supply chains remain vulnerable to disruptions, and the slowing momentum of resilience-building efforts raises questions about long-term strategies.
As companies navigate these challenges, the future of global supply chains may depend on a blend of innovation, investment, and pragmatism. Whether nearshoring represents a transformative shift or a temporary response to past shocks remains an open question. What is certain is that the path forward will require balancing global collaboration with regional autonomy, ensuring supply chains remain agile in an increasingly interconnected and unpredictable world.